In a world of ever-evolving and ever-improving technologies, nothing stays the same for long. As asphalt batch mix plant manufacturers incorporate new technological advancements into their existing products, they bring new plants with new designs to the market. Consequently, there are plenty of plants to choose from; new and old alike.
With this in mind, it makes sense to learn about the minimum features that a typical batch mix plant will come with. This knowledge will help you understand the capabilities of various asphalt batch mix plants you might be interested in purchasing.
Herein we will explore the features of an asphalt batch mix plant:
Salient Features A Batch Mix Plant Has
#1. Dryer Drum
The dryer drum is used to dry the asphalt, typically by blasting the aggregate with hot air streams. For the best results, the dryer drum is insulated and optimized to evenly distribute the materials. A such, while the cylinder rotates, the aggregate tumbles in the dryer drum with hot air blasting through the drum, elevating the temperature in the aggregate and getting rid of any moisture lingering the aggregate.
#2. Burner
The burner is the main energy source in the plant. It can use diesel of heavy oils with controls to regulate the flame length.
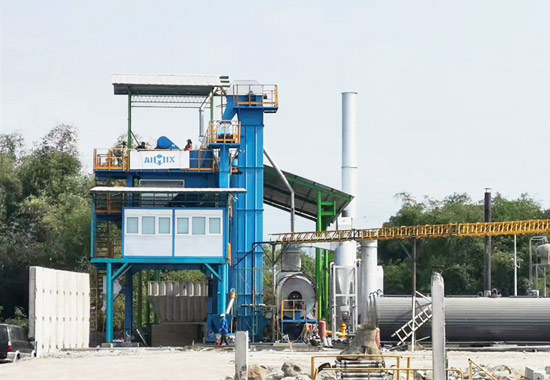
#3. Batching Tower
The batching tower is the main feature of a batching plant. Typically this part of the plant is automatically controlled to ensure consistency in the final product. The batching tower consists of various equipment such as an asphalt weighing unit, the mixer, the elevator, the vibrating screen for screening the inputs, the mineral filler elevator, the aggregate storage bins, and the asphalt batch weighing unit.
#4. Cold Feed Bins
The cold feed bins are used to accurately meter the different aggregates before being fed to the drying drum. This is an important feature as it allows plant managers to create asphalt of different qualities and characteristics with exceptional efficiency.
#5. Control Unit
Modern-day asphalt batch mix plants are run from a centralized control unit. From the control unit, the plant manager can control every aspect of the production process right from the user-friendly control panels and monitors. Importantly, having a centralized control unit reduces the labor required to run the plant. Typically the control unit will allow the plant manager to control the burner, the damper, the temperature, the start and stop sequences, the emergency procedures, and any other necessary function.
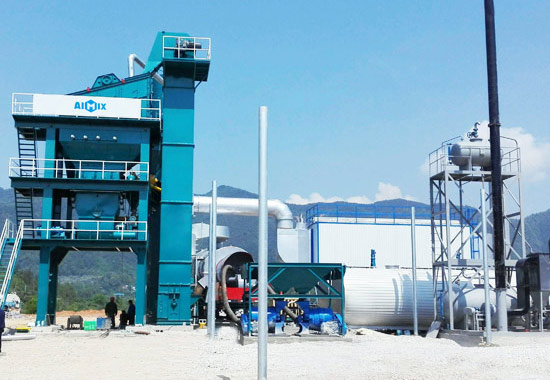
# 6. Bitumen Tank
The bitumen tank is an insulated tank that holds the bitumen during the production process. It is heated with thermal or diesel and it typically has automatic temperature adjustment and control. Moreover, it has suitable valves that control the transfer, charge, and discharge of the bitumen.
#7. Wet Dust Collector/Bag House Filter
The bag house, also known as the wet dust collector filter and removes the dust from the dryer’s exhaust to reduce the amount of dust emitted to the environment. This feature is fitted with a safety device that allows for automatic or manual temperature adjustments and controls. Moreover, they typically use counter-flow cleaning for improved efficiency.